What prompted significant changes in the ramen market in 2024? A notable shift in consumer preferences and quality control measures heavily influenced ramen brands in 2024.
A recall in 2024 within the ramen industry involved one or more brands, potentially due to safety concerns regarding ingredients or production processes. This event necessitates a reevaluation of ingredients, manufacturing standards, and quality control procedures. For example, if a specific type of MSG used in a certain brand was found to be contaminated, the entire batch of ramen products that used this particular MSG would likely be recalled. Such recalls can affect consumer confidence in the brand and demand for their products.
The 2024 recalls, while impacting specific brands, highlight the importance of stringent quality control measures in the food industry. They also underscore heightened consumer awareness regarding food safety and quality. This event compels the industry to continuously improve its standards and transparency to maintain customer trust. The impact of recalls extends beyond the affected brands, potentially influencing consumer behavior, promoting industry-wide improvements in safety protocols, and influencing future business strategies in product formulation and manufacturing.
Understanding the specifics of these recalls, including the affected products, causes, and the extent of the market impact, requires analysis of public records and industry reporting. Detailed insights can be gathered by examining the reactions of consumers and competitors, and by studying the aftermath of previous food safety concerns. Investigating the evolving regulatory landscape and how it impacts brands' practices will also provide a clearer picture of the issues at play.
Ramen Brand Recall 2024
A significant event in the ramen industry, a 2024 brand recall, underscored the critical need for rigorous quality control measures and consumer safety protocols. Understanding the factors behind this event is essential for navigating the complexities of food safety and consumer confidence.
- Contamination
- Ingredients
- Safety
- Production
- Consumer Trust
- Reputation
The 2024 recall highlighted potential contamination issues, impacting ingredient quality and manufacturing processes. This necessitates strict safety standards in production. Consumer trust was damaged, and the brand's reputation suffered. Subsequent recalls might involve different aspects, like flawed packaging or mislabeling, emphasizing the multifaceted nature of quality control. For instance, a recall due to contaminated MSG might influence consumers' choices, emphasizing their concern for specific ingredients. Addressing such issues requires proactive quality assurance throughout the supply chain and clear communication with consumers.
1. Contamination
Contamination, a critical factor in the 2024 ramen brand recall, represents a significant threat to consumer safety and brand reputation. This contamination could manifest in various forms, including microbial contamination, chemical contamination from ingredients or manufacturing processes, or physical contamination with foreign objects. The presence of harmful substances compromises the safety and quality of the ramen product, potentially leading to serious health consequences for consumers. This issue highlights the importance of rigorous quality control measures throughout the entire supply chain, from ingredient sourcing to final product packaging.
Real-life examples of such contamination issues include instances where contaminated ingredients, such as tainted MSG or improperly processed wheat, were used in ramen production. Contaminated water sources can also contribute to the presence of harmful pathogens in the final product. The recall likely resulted from detecting these contaminants in the tested products, or from reporting by consumers experiencing adverse reactions. Tracing the source of contamination and implementing corrective measures are crucial for preventing future incidents. This requires meticulous record-keeping, regular testing of raw materials and finished products, and strict adherence to sanitation protocols in manufacturing facilities.
Understanding the connection between contamination and recalls in the ramen industry is vital for maintaining consumer trust. Robust quality control procedures, proactive contamination prevention strategies, and transparent communication are essential components in safeguarding consumer well-being and preserving brand integrity. The prompt and effective response to contamination incidents, including product recall and corrective actions, can lessen the negative impact on the brand's reputation and customer confidence. This proactive approach ensures industry resilience and customer satisfaction. Failure to address contamination concerns adequately can lead to significant financial losses, legal repercussions, and lasting damage to the company's image.
2. Ingredients
Ingredient quality and safety are paramount in food production, particularly in the context of a ramen brand recall. The sourcing, handling, and processing of ingredients can directly impact product safety and consumer health. A recall in 2024 potentially stemmed from issues related to ingredients, highlighting the crucial role they play in maintaining consumer trust and product integrity.
- Contaminated Raw Materials
Inadequate quality control in sourcing raw materials can lead to contamination. This might involve tainted flour, contaminated water used in the production process, or improperly stored ingredients. For example, if a supplier provided tainted wheat, the resulting ramen would be unsafe for consumption. Such issues directly contribute to product recall as a critical response to protect consumers.
- Inappropriate Ingredient Use
Using ingredients beyond their expiration dates or employing incorrect ratios can compromise product safety. For instance, insufficient or incorrect amounts of a critical ingredient like MSG could affect taste or have unintended health consequences. Furthermore, incorporating ingredients not listed on product labeling or exceeding maximum allowed levels can result in recalls as regulators demand adherence to strict guidelines.
- Allergen Management Issues
Failure to manage allergens correctly can pose a significant risk to consumers. Ramen recipes containing ingredients that can trigger severe allergic reactions require thorough allergen labeling and separation measures during production to prevent cross-contamination. A recall might occur if products contained unlisted allergens or if cross-contamination protocols were breached.
- Unvetted Suppliers
The reliability and quality of ingredient suppliers significantly impact product safety. Working with unvetted suppliers may lead to the use of contaminated or inferior ingredients, which can lead to a product recall. Strict supplier vetting processes and quality assessments are vital in preventing such issues, especially in cases where ingredients pose significant safety risks.
These issues associated with ingredients demonstrate the significant link between ingredient sourcing and quality control and the subsequent need for recalls. The 2024 ramen brand recall serves as a reminder of the crucial role of safe ingredient selection, handling, and processing in maintaining consumer trust and the industry's reputation. Companies must implement rigorous measures across their supply chains to ensure ingredient safety, transparency, and compliance with regulations to avoid future incidents.
3. Safety
A ramen brand recall in 2024, stemming from concerns over safety, underscores the critical role of safety in the food industry. Product safety directly impacts consumer well-being and brand reputation. Safety is not merely a desirable attribute but a fundamental requirement in food production. Failures in maintaining safety standards have significant consequences, ranging from reputational damage to legal ramifications. The recall highlights the interconnectedness of safety protocols, ingredient sourcing, production processes, and consumer confidence.
Real-world examples illustrate the importance of safety measures. If a recall arises due to contaminated ingredients, like tainted wheat or improperly processed MSG, consumer health is directly threatened. Subsequent adverse reactions or health complications could necessitate expensive and prolonged interventions. A lack of meticulous ingredient checks, inadequate sanitization procedures in manufacturing, or flawed packaging designs contribute to potential safety hazards. These incidents highlight the potential for serious consequences when safety protocols are overlooked or implemented inadequately. Effective quality control measures are vital to avoid such incidents. Regulatory bodies play a pivotal role in safeguarding consumer health and enforcing these standards. The impact of a recall extends beyond the immediate affected consumers, encompassing the entire supply chain, affecting distributors, retailers, and the brand's reputation for reliability and trustworthiness.
In conclusion, safety is an integral component of any successful food brand. The 2024 ramen brand recall emphasizes the potential for significant damage when safety standards are compromised. Understanding the cause-and-effect relationship between safety protocols and recalls is essential for maintaining consumer confidence, upholding brand integrity, and preventing future incidents. Maintaining meticulous quality control throughout the supply chain, from ingredient sourcing to product packaging, is paramount in preventing safety-related recalls. Effective communication with consumers about safety measures and product recalls is equally critical in mitigating the fallout and preserving brand trust.
4. Production
Production processes are directly implicated in food safety and quality, and a 2024 ramen brand recall likely stemmed from issues within these processes. Understanding these facets is crucial in analyzing the recall and preventing future incidents.
- Sanitation and Hygiene Standards
Manufacturing environments must adhere to strict sanitation protocols to prevent contamination. Inadequate sanitation practices can introduce harmful microorganisms or foreign objects into the final product. Compromised hygiene, whether due to insufficient cleaning procedures or inadequate equipment maintenance, can lead to contamination, thus necessitating a recall. Examples include improperly cleaned equipment leading to the spread of bacteria or inadequate handwashing protocols introducing pathogens.
- Equipment Maintenance and Calibration
Regular maintenance and calibration of production equipment are essential to ensure consistent product quality and prevent malfunctions. Malfunctioning equipment, such as faulty mixers or improperly calibrated weighing scales, can result in inconsistent product composition or improper ingredient ratios, potentially compromising safety or quality. A recall might follow if quality control procedures detected defects that could harm consumers or compromise the product's intended properties.
- Ingredient Handling and Mixing Procedures
Proper handling and mixing of ingredients are vital. Inadequate protocols for handling raw materials or faulty mixing procedures could lead to uneven distribution of ingredients or contamination. Inconsistent mixing might cause variations in taste, texture, or nutritional content, while improper handling could lead to microbial contamination of the product. If such issues were discovered during quality assurance testing, a recall becomes a necessary precaution.
- Packaging and Sealing Processes
A key aspect of product safety involves proper packaging and sealing to prevent contamination and maintain product integrity. Defective packaging, improper sealing, or insufficient protection from external contaminants could compromise the product's safety or quality. For example, if the packaging was improperly sealed, allowing moisture or pathogens to enter, a recall would become necessary.
The 2024 ramen brand recall likely involved one or more of these production-related factors. Examining these elements reveals the importance of meticulous process controls and continuous monitoring during manufacturing. Without stringent quality checks, products may become compromised, prompting recalls and ultimately affecting consumer trust and brand image. A proactive approach to production safety, encompassing strict adherence to hygiene, equipment maintenance, ingredient handling, and packaging protocols, is crucial for preventing future incidents.
5. Consumer Trust
Consumer trust is a cornerstone of any successful brand, particularly in the food industry. A ramen brand recall in 2024, stemming from potential safety or quality issues, profoundly impacted consumer trust. This underscores the vital link between product quality, safety, and consumer confidence. The erosion of trust, once established, can be challenging to rebuild, often requiring significant investments in corrective actions, enhanced transparency, and unwavering commitment to future quality control.
The recall likely triggered a decline in consumer confidence in the affected brand. Consumers may have experienced negative emotional responses, impacting their willingness to purchase products from the same brand. Furthermore, the recall may influence perceptions of the wider industry. The extent of this impact varies depending on factors such as the severity of the issue, the promptness of the recall, and the transparency of the brand's response. In situations where a recall highlights systemic issues rather than isolated incidents, consumer confidence in the entire industry could suffer. Real-life examples demonstrate this impact: a significant recall can lead to a dramatic drop in sales for the affected brand, potential stock price fluctuations, and a loss of market share. Moreover, the recall may trigger negative publicity, further diminishing consumer trust. This negative perception necessitates swift and comprehensive corrective measures to minimize long-term harm and regain consumer confidence.
Understanding the connection between consumer trust and brand recalls is crucial for brands in the food sector. Effective strategies to maintain and regain consumer trust involve transparency, prompt action, and demonstrable commitment to quality control. Fortifying consumer trust through robust safety protocols, meticulous ingredient sourcing, and transparent communication is essential for long-term sustainability and market success. Brands must recognize that rebuilding trust often requires more than just addressing the immediate issue; it demands sustained efforts to reassure consumers that safety and quality are prioritized. The 2024 recall serves as a critical reminder of the immense value of consumer trust and the profound consequences of jeopardizing it.
6. Reputation
A ramen brand recall in 2024 significantly impacted brand reputation. A company's standing with consumers is directly tied to its products' safety and quality. A negative incident, such as a recall, can drastically alter public perception and trust, potentially leading to long-term consequences for the brand's market presence.
- Erosion of Consumer Trust
A recall signals potential safety concerns, undermining consumer confidence in the brand's products. Consumers may associate the brand with compromised quality, potentially affecting purchasing decisions in the future. Past instances of recalls, especially if not addressed effectively, often result in sustained damage to consumer trust, even after the immediate crisis has passed.
- Damage to Brand Image
A recall can tarnish the brand's image. Consumers may view the brand negatively, associating it with risk or negligence. The perception of carelessness in product safety, even if the recall results from a single incident, can severely harm the brand's reputation. This reputational hit can encompass decreased brand loyalty and a reduced positive perception within the industry.
- Financial Implications
Loss of consumer trust and a damaged brand image often translate to significant financial repercussions. Decreased sales, loss of market share, and reduced investor confidence are potential outcomes. The cost of rectifying the issue, including recall procedures and consumer compensation, can be substantial. Brand equity, a crucial asset reflecting public trust, is eroded, leading to lower valuations and difficulties in attracting investment.
- Impact on Industry Reputation
A notable recall can cast a shadow over the entire industry. Consumers may perceive the entire sector as less trustworthy, impacting overall market confidence. This generalized perception of risk can deter consumers from purchasing related products from other brands, negatively influencing the industry's overall reputation. If the recall highlights systematic issues, the entire industry may face a reputational crisis.
The 2024 ramen brand recall serves as a stark reminder of the vital connection between product quality, safety, and reputation. A recall not only impacts the immediate affected brand but can also cast a wider net over the entire industry. Companies must prioritize stringent quality control and transparent communication with consumers to safeguard their brand reputation. Building and maintaining trust with consumers is crucial for long-term success and sustainability within the food industry.
Frequently Asked Questions
This section addresses common inquiries regarding the 2024 ramen brand recall, providing factual information and clarification.
Question 1: What was the primary cause of the 2024 ramen brand recall?
The specific cause of the 2024 recall varied depending on the affected brand. Possible causes included contaminated ingredients, improper handling during production, or issues with packaging. Comprehensive investigation into each recall revealed the underlying reasons for the necessary actions.
Question 2: How did the recall affect consumer trust?
The recall undoubtedly negatively impacted consumer trust in the affected brands. Consumers may have experienced concerns regarding the safety and quality of future products. A loss of consumer confidence often necessitates significant efforts to rebuild trust and regain market share.
Question 3: What steps did the affected brands take to address the recall?
Affected brands typically initiated a recall process, removed the affected products from shelves, and communicated with consumers via appropriate channels. They also often conducted thorough investigations into the cause of the recall to prevent future incidents.
Question 4: Were there any regulatory actions associated with the 2024 recall?
Regulatory bodies frequently investigated recalls and implemented measures to strengthen safety protocols within the industry. This may involve updated guidelines, increased inspections, or enhanced safety standards for suppliers and manufacturers.
Question 5: What lessons were learned from the 2024 ramen brand recall?
The 2024 recall emphasized the critical importance of rigorous quality control throughout the supply chain, from sourcing ingredients to manufacturing and packaging. Increased transparency and adherence to regulatory guidelines are vital aspects of maintaining consumer trust and safety standards.
Understanding the 2024 recall and its implications highlights the ongoing need for meticulous vigilance and robust quality control in the food industry to protect consumers and maintain brand reputation.
Moving forward, analysis of the recall can offer valuable insights into the importance of risk assessment, proactive quality control measures, and effective communication in mitigating similar issues.
Conclusion
The 2024 ramen brand recall served as a stark reminder of the critical importance of stringent quality control and safety protocols in the food industry. The event underscored the interconnectedness of ingredient sourcing, production processes, packaging, and consumer trust. Issues related to ingredient contamination, inadequate sanitation practices, and flawed equipment maintenance were identified as potential contributing factors. This highlights the potential for significant reputational damage and financial losses when these protocols are compromised. The recall emphasized the necessity of meticulous oversight and preventive measures throughout the entire supply chain, from raw material procurement to final product distribution.
The aftermath of the 2024 recall should prompt a broader reflection on industry best practices. Thorough safety audits, enhanced ingredient testing procedures, and transparent communication with consumers are vital in mitigating risks and fostering continued public trust. The industry must prioritize preventative measures and proactive quality assurance to avoid future incidents and maintain the long-term viability of the market. Regulatory agencies must also play a crucial role in enforcing standards and ensuring accountability, ultimately safeguarding consumer health and well-being.


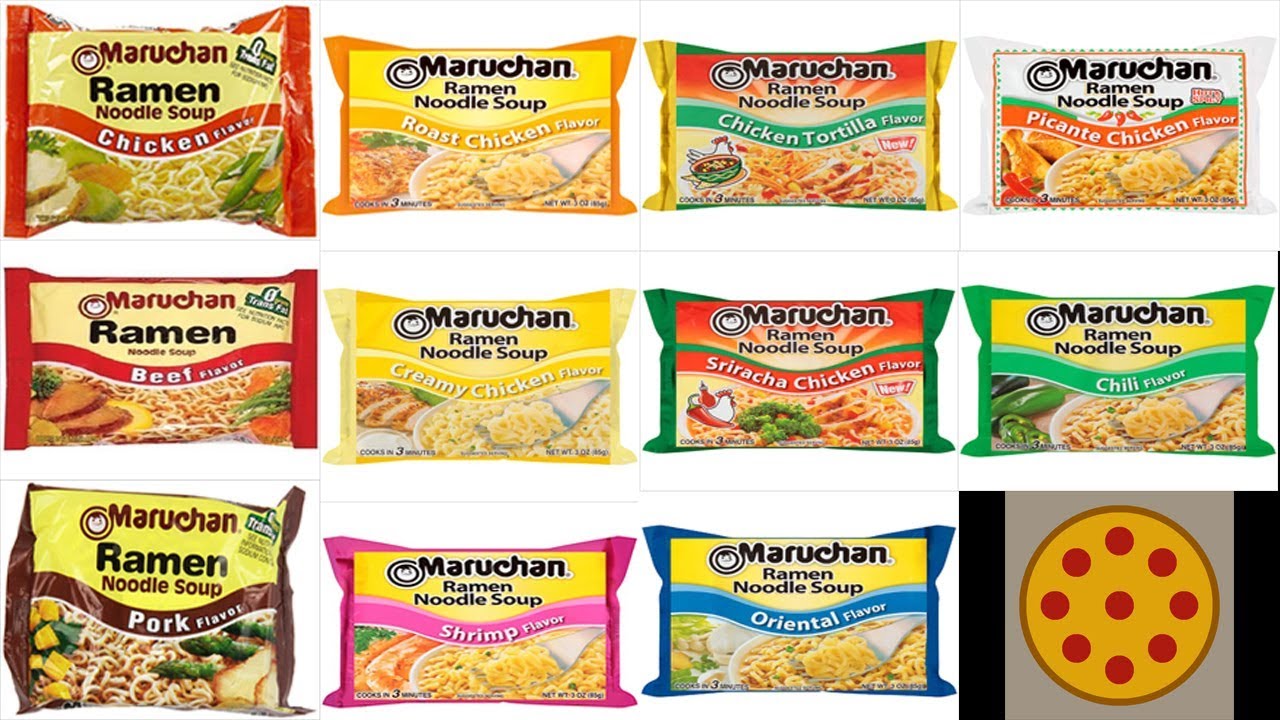